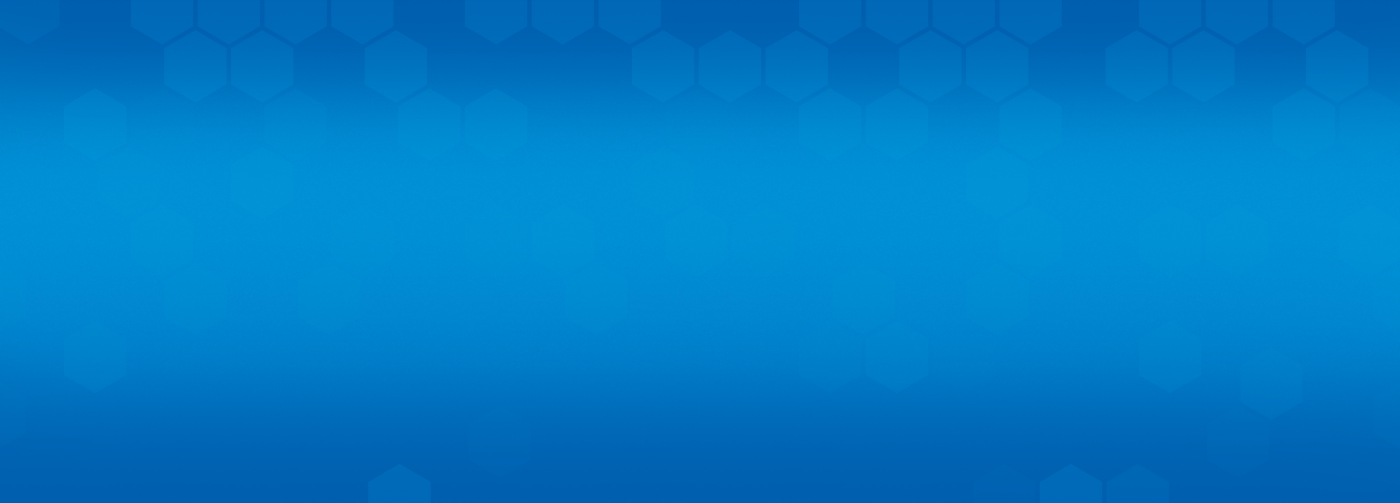
Fluidics
Modeling fluidic flow is essential when considering development costs and time to market. Without a preemptive and proactive fluidic analysis, the product development approach inevitably used is “cook-and-look.” This happens when one designs a fluidic system, orders the fluidic system, tests the fluidic system, and hopes that it works on the first run. Experience shows that the cook-and-look approach will unavoidably result in multiple prototype iterations, significantly increasing costs and delays to market.
Using computational fluid dynamic modeling, IDEX Health & Science offers instrument developers an option to analyze how their fluidics will operate before committing to expensive prototypes. Developers in this space can characterize the functionality of their hardware in weeks instead of months in the prototyping feedback loop. Start your project on the right foot with fluidic simulation and modeling with IDEX Health & Science.
The diagrams below are computational models simulating fluid flow rate, pressure, forces, and mechanical stress run on complex flow paths.
Figure 1: Slice von Mises stress (psi); Surface von Mises stress (psi).
Figure 2: Surface pressure (psi); Surface shear stress (psi); Arrow volume velocity field (spatial frame); Surface contact pressure (psi).