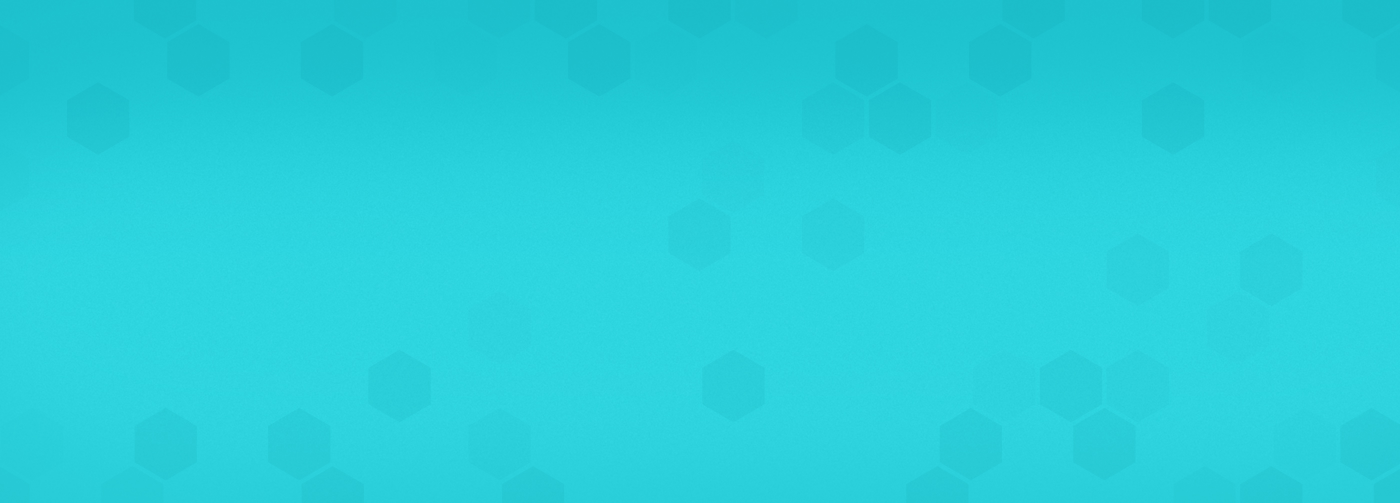
Here we have provided comprehensive lists of commonly asked questions regarding our fluidics products and related applications. This information is designed to support your inquiries, but if you don’t find the answers you are looking for we encourage you to contact us for further assistance.
Please use the sort buttons in the left navigation to navigate between questions and answers that are specific to our Optical Filters, Optical Imaging Systems, Cameras, Microfluidics, Webstore, and Engineering Partnership.
The most important step in preserving the life of your column is to use clean solvents and samples. This can be done primarily through the use of filtration. Utilizing solvent filters, both in the reservoir and inline as well as sample filters, can help keep the particulate matter that may be present in these chemicals out of your column.
Another concern you must be careful to keep in mind is proper care of your column. Many times a buffer may be used as part of your mobile phase, and depending on the type of buffer you use, if it is allowed to sit stationary for a relatively long period of time, some of the buffer may precipitate out and plug your column. As a general rule, you are going to leave your column unused for more than 24 hours and you are using a buffer that might precipitate, take a few moments to wash your column free of the buffer. For most columns, it is best to store the column filled with an organic solvent, like methanol or acetonitrile. However, make sure these chemicals are compatible with the stationary phase inside your column, because if you use the chemicals that aren’t compatible with your stationary phase, your column can be functionally destroyed.
As a final note, one of the best ways to insure longer functional life from your column is to use a guard column. Guard columns often have similar chemical stationary phases as the analytical columns with which they are being used. Therefore, if something in the samples or in the mobile phase can cause damage to your analytical column, that something will interact with the stationary phase within the guard column first, hopefully saving any major damage to your analytical (and more expensive) column.
Most thermoplastics including acrylic, PVC, Ultem® polyetherimide, and polycarbonate.
Diffusion bonding is a thermal process that fuses layers of material together, forming a permanent bond. Depending on your application requirements, IDEX Health & Science can bond many clear and colored materials like acrylic and GE Plastics’ Ultem® polyetherimide. We may be currently bonding material you are using or may have diffusion bonded prototypes on hand (or in stock).
IDEX Health & Science also employs other bonding methods that may be more appropriate for your application, like adhesive bonding, and solvent bonding.
A sample is separated into its components due to a process termed differential migration. This migration is controlled by the degree of attraction each component has for the stationary phase compared to the mobile phase. Usually, the various components that make up a sample will exhibit varied degrees of attraction, and it is based on these varied levels of attraction that separation takes place.
Optimal separations can be achieved by making strength adjustments to the stationary and/or mobile phases and selecting the right chemistries for these two phases can enhance the differential migration of the sample components.
The mobile phase refers to the solvent mixture being pumped through the column. Because it is moving on a continuous basis, it is referred to as mobile.
Mobile phase chemical properties are often different than stationary phase properties. The difference between the properties is used to dictate the type of separation that takes place; therefore, optimal sample component separation is achieved through the use of the appropriate stationary phase and mobile phase compositions.
HPLC systems can be as varied as the type of analyses that can be performed. However, the typical system can be broken down to some basic components which are easily identified in most systems. The best way to identify system components is to follow the flow path of the mobile phase from beginning to end. First, there is the MOBILE PHASE RESERVOIR, which houses the solvent mixture used during the analyses.
The second component is the PUMP, which offers back-pressure regulator controlled flow of the mobile phase through the rest of the system. In most instruments, the mobile phase is degassed prior to entering the pump to reduce dissolved oxygen and bubbles, which can negatively impact chromatography results. This is often done by flowing the solvent through a DEGASSER comprised of a gas permeable membrane and vacuum source. Incidentally, it is vitally important that a pump function very well in order to insure reproducibility in chromatographic data.
The third component is the INJECTION VALVE, used to introduce a set volume of sample into the solvent stream.
Fourth is the COLUMN, often referred to as the “heart” of the HPLC system. It is here that the actual separations occur; without the column, no usable data can be obtained.
Fifth in the system is the DETECTOR. This instrument is vital, as it generates an electronic signal that can be interpreted into a trace. Quantifiable data is obtained by thorough examination of this trace.
Sixth is the WASTE RESERVOIR. Here the mobile phase and analyzed samples collect after passing through the rest of the system.
Last in our basic breakdown of an HPLC system is a RECORDER. While solvent does not come in contact with or pass through this instrument, the recorder is responsible for translating the electronic signal being generated from the detector into a printed trace, referred to as a chromatogram. Using mathematical formulas, analytical information can be gleaned from this chromatogram.
Assuming the noise along your baseline is not due to anything electronic within your detector, there are two things that can be done to help minimize this problem.
First, you can adequately degas your solvents. Following the flow path, the solvent stream moves quickly from a high-pressure environment within the column to a low-pressure environment on the effluent side of the column. Often, if solvents are not properly degassed, the gases being forced to remain dissolved in solution due to the high pressure inside and upstream from the column quickly outgas when the pressure changes. This outgassing is visible in the form of bubbles in the solvent stream line. These bubbles can pass into your flow cell, and once there they can cause excessive noise. Adequate degassing can help eliminate the problem of outgassing and thus help eliminate the chance of bubbles forming in the flow cell.
The second thing you can do to help eliminate this problem is to use a back pressure regulator on the effluent side of your flow cell, because one of the primary factors causing bubbles to form in the solvent stream is the drastic drop in pressure the solvent experiences. Using a back pressure regulator forces additional pressure along the flow path, thus helping to ensure that any gas dissolved in the mobile phase stays dissolved until it has passed through the detector flow cell.
Several things can replace stainless steel parts in bioinert situations. If you are looking to continue using metal, then in some cases titanium is an acceptable alternative. However, titanium is brittle and very difficult to cut, and in the case of tubing, it is very expensive.
For other purposes, almost universally, PEEK is a fantastic alternative to stainless steel. PEEK, or polyetheretherketone, can be used in high-pressure situations like stainless steel, and it is compatible with most chemicals used in HPLC. PEEK tubing is less expensive than stainless steel, easier to cut and more flexible. PEEK fittings are appropriate to be used with most all instruments. PEEK fittings offer high-pressure holding capabilities, and typically only need to be tightened finger tight, minimizing the need for special tools.
A guard column is almost always recommended for use in your system, especially when you have components in your sample that may harm your sensitive stationary phase. At times you may find that some components in your sample seem to permanently bond with your stationary phase, eventually decreasing the efficiency and usefulness of the column, forcing early replacement.
When using a guard column packed with a similar stationary phase to that of your primary analytical column, it is possible to significantly increase the life of your column.
The guard column is a relatively low-cost product, designed to selectively filter out those components that might cause damage to your primary column. By allowing the harmful components in your sample to interact with its stationary phase material, the guard column keeps those components from exerting their effects on your analytical column’s packing. However, keep in mind that because the harmful components of your samples are interacting with the guard column, it must be replaced from time to time. This can be monitored by keeping track of the back pressure exerted by your column system. When the back pressure increases significantly, that should serve as a good indicator that it is time to replace your guard column.
The IDEX Health & Science Column Couplers are assembled using either our stainless steel or PEEK tubing in conjunction with Fingertight fittings. These universal couplers permit the lowest swept-volume connection of any coupler on the market, offering zero loss of column efficiency. These couplers will connect any column with 10-32 coned internal threads to a pre-column or guard column with the same threads.
We also have a single-piece coupler available. For more information, contact your local IDEX Health & Science Distributor or IDEX Health & Science directly.
Dead volume is defined as that portion of the flow path which is not directly inline,that is, unswept. It is these small spaces within your system where remixing of the separated sample bands occur, or where the initial sample is diluted with mobile phase. Dead volume should be minimized in a system, especially when small-volume columns of high plate numbers are used. Many times, dead volume can manifest itself through poor analytical data, often seen as split peaks or broad peaks on your chromatogram.
It is important to note that “dead volume” does not typically refer to the overall internal volume of a product or system. Usually, at least some portion of the pathway through a product is directly in the flow path — this volume is typically referred to as “swept volume.” For proper reference to the total internal volume, the term “void volume” should be used.
Pump check valves are mechanisms designed with a special seal internal to its structure, one that allows solvent flow to proceed in only one direction. They are usually placed on both sides of the pump head, such that when the piston draws back to fill the pump head with fresh solvent, it does not pull back on the already expelled solvent. And when it expels the solvent it has taken in, it does so only in the direction of the fluid path, not back into the solvent reservoir.
Some check valves use a dual ruby ball and sapphire seat combination internally. The first set is designed to provide the primary sealing surface inside the check valve, while the second combination is designed as a backup to the first, in the event the first one should fail. The use of this sealing technology incorporates the pressures generated by the pump and your system to force the ruby ball against the sapphire seat, creating the seal needed by your pump.
An inline solvent filter can make a very useful and protective addition to your system. Placing it between the pump and the injector, an inline solvent filter can protect your injector and the rest of your system—including your column and flowcell—from most particulate matter that exists in your solvent stream.
Where does this particulate matter come from? One source is from your solvent itself. If you have not pre-filtered your solvents, or if you don’t use a solvent filter in your reservoir(s), there is a good chance that some particles are present. Another source of contaminants is the pump seals themselves. As your pump’s pistons move back and forth through the seals, the friction created can cause small particles of seal material to fleck off and enter the solvent stream.
When any of this particulate matter passes on to your injector valve, it may get held up within the small passageways built into the valve’s seal. Once this occurs, it can cause flow blockages which may result in poor or no sample being injected. It may also result in the blocking of the solvent stream, which would be evident in a high pressure build up. One of the worst scenarios that can occur, however, is that the contaminant lodges between the seal and the inner face of the valve itself. As the valve rotates back and forth on subsequent injections with this particulate matter between the seal and valve face, both the seal and the valve face can become scored permanently. A scoring on either of these surfaces can allow fluid—either the sample or the solvent stream—to begin flowing in places it should not, usually resulting in a leak of fluid from the valve itself.
If the contaminants should happen to pass through the injection valve and continue on along the flow path, they could possibly enter the column, where they can ultimately cause poor chromatography.
Some gases, like oxygen, nitrogen and carbon dioxide, have a tendency to dissolve into solution at a much greater rate than do inert gases such as helium. Even though they do have a higher solubility in most solvents, they often do not have equal solubility in all solvents.
What does this mean to visible quality performance of your equipment? If you are running an isocratic method, pulling your pre-mixed solvent from one reservoir only, then it probably doesn’t mean much in reduced performance. However, if you are running any method that pulls solvents from multiple reservoirs, it can result in the formation of bubbles in your solvent line.
One very helpful way to keep the amount of dissolved gas in your solvents very low is through sparging. The sparging process forces an inert — and virtually insoluble — gas into a solution, driving out dissolved gases from the solvent. This helps prevent the formation of bubbles in your flow stream, helping to produce better chromatographic results.
PEEK tubing is extremely flexible and can be easily cut to your desired lengths with the IDEX A-327 Tubing Cutter. This tubing can be used with stainless steel nuts and ferrules, flangeless fittings, or any IDEX Health & Science universal Fingertight fitting. PEEK tubing can also withstand very high temperatures, and has a recommended maximum use temperature of 100°C, above which the tubing will hold to lower pressures.
PEEK tubing, even though it is polymer-based, can withstand pressures up to 5,000 psi or higher in many cases (dependent on the ID of the tubing; larger IDs require a lower maximum pressure rating. The solvent being used can also effect pressure ratings). Another nice benefit of this tubing is its very smooth internal surface, which cannot be matched by any stainless steel tubing and which minimizes the turbulence created by laminar flow of the fluid.
Very few solvents have been shown to not be compatible with PEEK. Two common solvents are known to directly attack the material: concentrated sulfuric acid and concentrated nitric acid. Other less common solvents that attack PEEK polymer include: halogenated acids such as hydrofluoric acid; hydrobromic acid; hydroiodic acid (hydrochloric acid is approved for use in most applications); and pure halogenated gases. There are a few other chemicals that exhibit a physical swelling effect on PEEK tubing, namely methylene chloride, DMSO, and THF. However, these chemicals do not adversely affect PEEK fittings. Please see our Chemical Compatibility chart.
Because the list of adverse chemicals is so short, PEEK is an excellent alternative to most other materials available commercially today, including stainless steel and titanium, as well as other polymers.
PFA tubing serves as an excellent replacement for PTFE Teflon, particularly where you are looking for similar physical properties—including lubricity—as those of PTFE, and where gas permeability, surface texture, and inertness are issues.
Additionally, a high-purity grade of PFA tubing is typically used when only the lowest level of polymer contaminants can be tolerated. This ultra-clean grade of PFA is often used in the medical industry.
There are two very common sizes of tubing you will find in HPLC. The most common size of tubing is 1/16″ outer diameter, or OD. You can usually find stainless steel and PEEK tubing of this size as part of your system. You might also find PFA or Tefzel® tubing of this size.
The other most common size of HPLC tubing is 1/8″ OD. Usually tubing of this size is used as solvent transfer tubing from the solvent reservoir to the inlet side of the pump. Most often, it is manufactured from Teflon.
There are other sizes of tubing you might find in an HPLC system, ranging from microbore tubing, with ODs that range from .004″ up to 1/16″, to larger 3/16″ OD tubing and even 1/4″ OD tubing.
A back pressure regulator is a device placed in the flow path after the detector to maintain a positive pressure on the effluent line leaving the column and the flowcell. Doing this helps minimize outgassing problems that often occur within the flowcell as the solvent in the flow path moves from the high-pressure environment of the column to the low-pressure environment (room pressure) after the column.
In addition, a back-pressure regulator can be used directly after a pump. In this configuration it will operate as a pump preload, and serve to help the pump operate more efficiently with less flow pulsation and/or disturbances.
One of the primary causes of slowly increasing pump pressure is the buildup of material on a filter or frit surface, forcing the pump to work harder to achieve the same flow rate. This build up is usually caused by particulate contamination in the mobile phase, solid particles from the sample being introduced into the system, or breakdown particles from seal surfaces, primarily the pump seal. Another source of increased pressure can be the slow deposit of impurities or other sample components that permanently bond with the stationary phase within the column. As this deposit increases, it takes more effort from the pump to push the sample and mobile phase through in order to maintain the set flow rate. In order to solve this problem, it is best to go through your system and change – one at a time – the filters and frits, and maybe even the column, until the pressure goes back to normal. Keep in mind that if you make a change on your system and the changed part does not improve your system’s performance, it is usually safe to put the original part back in and save your new part for a future necessary use.
As a general rule, stainless steel fittings are interchangeable initially, prior to the ferrule of the fitting being swaged into place. However, also as a general rule, once a stainless steel fitting has been swaged into place on a piece of tubing, it is best to use only that fitting with the mating part into which it was initially swaged.
The reason stainless steel fittings are not interchangeable after they have been swaged into place is due to what we will term “Dimension X.” This “dimension” refers to the length of tubing extending past the ferrule of a fitting that allows the tubing to have a flush connection at the bottom of the union or adapter into which it is being tightened. Depending on the manufacturer, this dimension can be longer or shorter than others. Keeping this in mind, let’s look at a couple of scenarios that might help explain this a little more in depth.
First, assume you have swaged a stainless steel nut and ferrule into a manufacturer’s union where Dimension X is long. Now, you remove the fitting from this union and try to attach it to another manufacturer’s union, where the requirements for Dimension X are short. Now your tubing extends past the ferrule too far, and no matter how much you tighten the fitting, you will never be able to create a seal between the outer surface of the ferrule and the inside surface of the union
In the opposite scenario, you swage a fitting into a manufacturer’s union where Dimension X is short. You then try to move this to a union where the required Dimension X is long. You are able to get a tight seal with the fitting, but you have introduced a dead volume chamber between the end of the tubing and the bottom of the union. Depending on the location of the union, this dead volume space can lead to remixing of your sample components and extra turbulence, among other problems.
Once again, as a general rule with stainless steel fittings, always use the same mated fitting initially used to swage one of these fittings in place.
If you are in a situation where you need interchangability, we recommends Fingertight Fittings. With Fingertight Fittings the ferrule does not permanently swage.
Please see our Fittings Primer for more information.
Fingertight fittings comprise a special category of fittings designed to replace stainless steel fittings. The first Fingertight fitting was designed and introduced to the HPLC market in March, 1984.
There are several types of finger-tightenable fittings on the market now, and the fingertight fittings have become very popular. There are several reasons for their popularity:
First is the convenience of fingertight fittings. It is convenient to be able to disconnect tubing without getting out the wrenches. Second, fingertight fittings are universal and the fitting does not attach permanently to the tubing. You can use the fitting in one receiving port, disconnect the tubing and fitting, attach the tubing to another manufacturer’s port and use the same fitting.
Third, since you are using your fingers to tighten the fitting, there is less chance of over-tightening (a major cause of leaks and hardware damage with stainless steel fittings). Lastly, fingertight fittings use a polymer (plastic) ferrule. The polymer ferrule does not score or scratch the cone in the mating fitting, so your fittings last longer. This is one of the reasons you should use fingertight fittings on your column — column end fittings and other mating ports will last longer with fewer leaks.
Use of the Super Flangeless ferrule systems manufactured by IDEX Health & Science. Through the use of a lock ring around the back of the ferrule, the ferrule system works like a seal and a bearing, preventing the twisting of the tubing and thus virtually eliminating the loosening of the fittings that occurs in some applications that use the standard flangeless fittings.
Available with PEEK or Tefzel ferrules for 1/16″ OD tubing and 1/8″ OD tubing. Also available with a Kel-F ferrule for 1.8 mm OD tubing.
We manufacture a variety of stainless steel, PEEK or Tefzel tees, Y’s and crosses designed to perform this function.
These products are engineered with small thru-holes to minimize the internal swept volume. Available in standard 10-32, 1/4-28 and 5/16-24 threads, these parts allow the connection of your tubing with standard Fingertight or flangeless fittings.
IDEX Health & Science carries a line of fittings that use PEEK tubing sleeve to allow the connection of capillary tubing to mating ports, with standard 1/16″ threads (10-32 style). The tubing sleeves are standard 1/16″ OD and are available as part of our standard product line.
To use the system properly, first insert your capillary tubing into an appropriately sized PEEK tubing sleeve, the sleeve ID approximately .002″ greater than the OD of your capillary tubing. Then slide the nut and ferrule over the sleeve. Next, push the tubing sleeve assembly into your port until it bottoms out, and tighten the fitting finger tight.
Additionaly, IDEX Health & Science has added a line of special FEP Teflon tubing sleeves for this same purpose. Functionally, they perform just as our PEEK tubing sleeves do; however, due to the relative softness of the Teflon tubing sleeves, standard SealTight Fingertight fittings may be used.
In most cases, these assemblies will hold to 6,000 psi.
Through the use of the IDEX Health & Science’s new Conical Adapter, you can create a union between your standard HPLC tubing and your peristaltic tubing. With this new adapter, 1/16″ or 1/8″ OD rigid tubing is connected to a fitting that allows peristaltic tubing to slide easily on and off of.
If you prefer something that makes a tighter connection with peristaltic tubing, you might try our P-757 or P-767 Peristaltic Tubing Adapters. These are specifically designed to facilitate the connection between 1/16″ OD rigid tubing and peristaltic tubing ranging in inner diameter from 1.22mm to 3.05mm.
IDEX Health & Science has created the Precolumn MicroFilter, the Inline MicroFilter and the Mini MicroFilter specifically for this purpose. Most of our MicroFilters utilize our MicroTight tubing sleeves along with two Micro-Fingertight fittings to accommodate most sizes of capillary or fused silica tubing. Two versions of our mini MicroFilter directly connect 360-380µm OD capillary tubing without the use of tubing sleeves.
The Precolumn and Inline MicroFilters retain particles larger than 0.5µm flowing through capillary tubing, with the use of a built-in 0.5µm PEEK frit. Capable of holding 5,000 psi of continuous pressure, these filters can be used in either high-pressure or low-pressure environments. The Precolumn MicroFilter has 10-32 male threads and is designed for direct-connecting into your microbore or other column. The Inline MicroFilter utilizes 6-32 threads for use with our Micro Fingertight fittings.
The Mini MicroFilter contains a thin stainless steel microscreen that offers a dramatic reduction in theoretical void volume, at only .085 microliters (includes frit volume). This filter is available with 1- and 2-micron porosity replaceable filter capsules, and employs a combination of a female nut and a specifically designed ferrule.
IDEX Health & Science has developed a line of Quick Connect Luer Adapters, allowing the connection of standard HPLC tubing utilizing commonly found thread dimensions: 1/4-28, 10-32 or M6. Central to the function of the adapter is a luer-lock connection in the middle of the part, such that you can split apart the union in the middle through a simple twisting action without disturbing the HPLC tubing connections on either end of the adapter.
Also, through mixing and matching, you can easily create an assortment of adapters to which you can connect a variety of standard fittings. Additionally, IDEX Health & Science has introduced the innovative LuerTight™ fittings system. This unique connector family allows a quick disconnection between 1/16″ and 1/8″ OD tubing without the need for threaded nuts to hold the tubing into place.
The Quick Connect Luer Adapters are available in either ETFE (Tefzel) or PEEK polymers; the LuerTight fittings are manufactured primarily from polypropylene.
IDEX Health & Science has offers a high-pressure, biocompatible Semi-Prep Inline Filter. It consists of a stainless steel body, two PEEK end fittings and a replaceable PEEK frit. Once you buy the unit, the only part that will need replacing is the PEEK frit inside. Available with either 2µm or 10µm frits. The 2µm version has a pressure drop of approximately 40-45 psi at a flow rate of 100 mL/min of water across the frit. The 10µm version has a pressure drop of less then 10 psi under the same conditions.
Please Note: our Semi-Prep Inline Filters are engineered to be used with 1/16″ OD tubing utilizing polymer fittings, such as our one-piece F-120 Fingertight fitting.
IDEX Health & Science offers Extender Tools that are especially useful to tighten or loosen IDEX Health & Science Fittings in hard-to-reach places. The tool’s design eliminates the potential problem of breaking off the heads of nuts. In addition, these product provide relatively uniform tightening of our Fittings into unions, tees, crosses and valves, taking the guess work out of the tightening process.
Our newer tools also have a 1/4 hex drive to attach to a torque wrench for an exact torque spec.
To help tighten our Headless Flangeless Nuts, IDEX Health & Science has developed a special Extender Tool, the P-297. This aluminum tool lets you easily tighten Headless nuts, thus improving their holding power.
The colored ring around the IDEX Health & Science frits actually do signify a micron size. Following is our color-coding:
We manufacture an assortment of nuts that utilize the M6 threads, which are standard for Pharmacia systems. The P-207, P-207S, P-226 and P-288 are manufactured to be used with 1/16″ OD tubing and can be used our 1/16″ flangeless ferrules.
The P-307, P-307S and P-326 are designed for use with 1/8″ OD tubing. These nuts are compatible for use with any 1/8″ flangeless ferrule available from IDEX Health & Science.
Please note, you can identify the metric flangeless nuts manufactured from IDEX Health & Science by a small mark (M6) molded directly onto a step on these nuts.
IDEX Health & Science manufactures polymer crosses out of PEEK and ETFE (Tefzel) which are engineered to be used with 1/4-28 flangeless fittings.
The P-634 and P-722 have a .020″ thru-hole, and are shipped with fittings designed for use with 1/16″ OD tubing.
The P-635 and P-723 have a .050″ thru-hole, and are shipped with fittings designed for use with 1/8″ OD tubing.
Use the IDEX Health & Science Pressure Relief Valve. By setting the internal cartridge to crack open at a pressure below the maximum pressure to which your syringe can be exposed, you allow a diversion of the flow to a waste container at any time the pressure on the flow path exceeds a safe operating pressure.
As experts in plastics machining, we’ll be pleased to answer your questions or help you understand the unique issues related to plastic machining, finishing, stress relieving, materials, assembly or other processing methods.
Your application, product development, and marketing requirements will determine the best plastic manufacturing method. There are twelve main considerations when determining whether to machine or mold your part.
IDEX Health & Science performs adhesive, diffusion (thermal), solvent, and ultrasonic welding.
Your application requirements, environment, materials, and bond strength demands will guide us in determining the best bonding method.
We can use a variety of bonding methods in your application such as adhesives, solvents, thermal methods, and ultrasonic welding. We may also advise that simple mechanical fasteners be used in place of gluing.
Through correct tool geometry, machine feeds and speeds, and annealing.
IDEX Health & Science spends a considerable amount of time developing tools, fixtures and machining methods that create the least amount of thermal and mechanical stresses. And finally, we have over 20 programmable annealing ovens that we use for intermediate and final stress relieving.
Many part failures that we see from other machining houses stem from improper or non-existent material stress management.
IDEX Health & Science utilizes vapor/chemical, flame, and mechanical methods to achieve desired surface finishes. We also use a variety of polishing/finishing methods to achieve the aesthetic and/or functional requirements for your part.
Usually, we’ll make every effort to get the best finish using our CNC machines. When surface finishes or optical/aesthetic requirements demand better than what our machines can provide, then we implement vapor and chemical polishing, flame polishing, or mechanical buffing. The method used is determined by the material type and the desired outcome.
It is important to note that we perform these operations on parts that we have manufactured, not on parts manufactured by others. That’s because control of residual stress, machining methods, etc. are critical to the success of any polishing method. If we have not manufactured the parts, we will not be confident that they have been manufactured correctly and can successfully be polished.
As a general rule, IDEX Health & Science can machine 0.006″ drilled holes, 0.010″ wide milled tracks, and hold tolerances down to ± 0.0002″.
Material type, part features, wall thicknesses, and other factors influence the low limits of machining possibilities.
In some applications, we can achieve 100:1 aspect ratios in drilled holes.
The best way to determine the smallest features that we can machine is to let us analyze your drawings and application requirements. We will then give you an educated answer as to what we can achieve for you.
Screw thread inserts may be a life-long source of stress in your part.
Screw thread inserts (STI) can cause continual radial stress in plastic because of the nature of how they are held in the material, but STIs can still be used in many applications. We recommend that ultrasonically installed inserts be considered as an alternative. The part will need to be annealed.
IDEX Health & Science would need to make a recommendation whether or not to use STIs after reviewing your application and material.
We offer most manual valve rotor seals in three standard materials: Vespel®, Tefzel®, and PEEK.
What are the pH ranges of the Vespel, Tefzel, and PEEK rotor seals?
The pH ranges are as follows:
If the needle seal located in the rotor seal is not sealing around the needle, some of the sample will come out of the injection port. The outer diameter and length of the needle must be the correct size for the valve in order for the needle seal to function. If the OD and needle length are correct, the needle seal may have expanded through frequent use. The needle seal can be reformed by pushing down on the needle guide, which in turn pushes on the seal and closes it up.
Note: Never use a beveled, pointed, or tapered needle. Always use a square cut needle. This can permanently damage the rotor seal and stator face assembly.
If your valve is leaking out the injection port, vent line(s), or the stator ring and stator interface, most likely the rotor seal has been scratched. When replacing the rotor seal, I always check the stator face assembly to make sure that it is not damaged. Any chip or crack on the ceramic stator face will damage a new rotor seal in just one turn. If the pressure setting of the valve has been exceeded, this can cause the valve to leak as well.
First, confirm that the EV/MXII valve will operate separately from your instrument. To isolate the valve, disconnect the interface cable from your instrument, leave the power supply connected to the unit, and put the unit in the LOCAL mode using the front panel.
To check the communications in the level logic mode:
To check the communications in the BCD mode:
If the valve is responding as described, the problem is with the instrument’s communication to the EV/MXII unit. Contact your instrument manufacturer’s technical service department.
Any instrument can be used to control an EV/MXII valve as long as it has external switches that are a contact closure or a TTL switch. Regarding the external switches:
Standard Fingertight fittings will not typically work. Making good connections in UHPLC applications will usually require either traditional stainless steel fittings or specialized fittings that have been engineered to work in the very high pressure environment of UHPLC. See our new MarvelX and MarvelXACT UHPLC Fitting Sets specially made for UHPLC applications.
Download the Fittings 101 Guide to learn more.