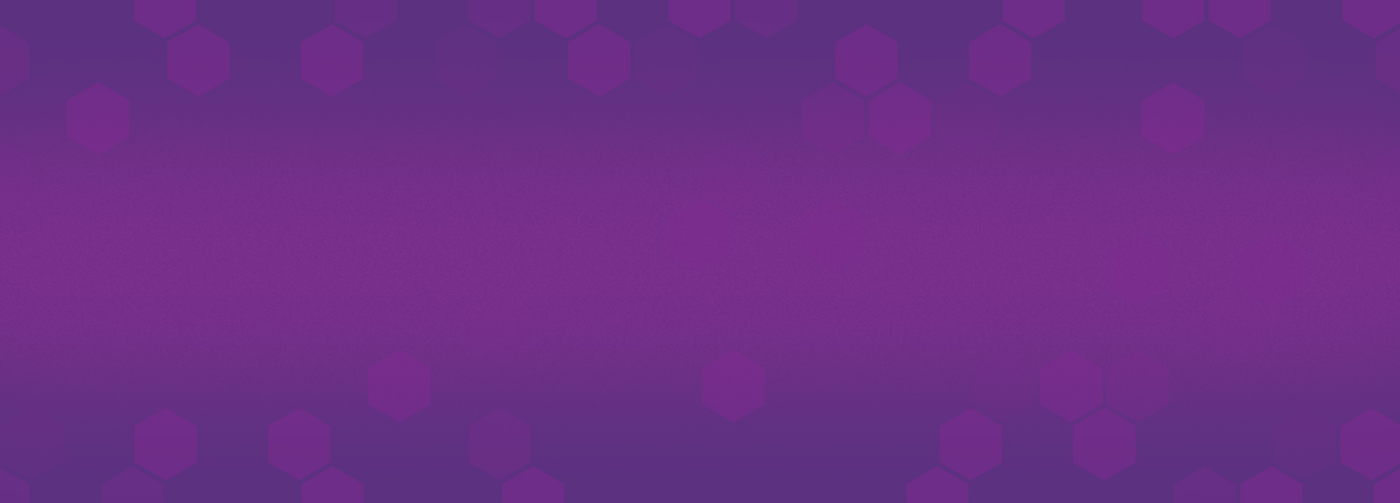
Fittings are typically comprised of a nut and a ferrule and have the important function of providing the physical connection of tubing throughout most systems. While simple in function, fittings exhibit some complexity regarding their description and how they are used.
Although restrictive in use and non-universal in application, stainless steel fittings are the most popular fitting used on HPLC systems today, due to their solvent inertness and high-pressure holding abilities. These fittings usually come in a conical configuration, requiring special care to be taken in choosing the proper fittings for any given mating port. To ensure proper operation and long life from the chosen fitting, it is best to use fittings specifically designed for use with a particular manufacturer’s port. Pictures of different nut and ferrule geometries are presented in the picture below.
Unlike their stainless steel counterparts, polymer-based fittings are typically nonrestrictive and fairly universal in function. Because of the nature of polymer-based fittings, the same degree of care does not have to be taken when choosing the proper fitting to mate with a specific manufacturer’s receiving port. Primarily, the only two characteristics of the fitting that must be known are the geometry (coned or flat bottom) of the receiving port and the thread dimensions. Polymer-based fittings also do not permanently attach (swage) to a piece of tubing and usually do not require the use of any tool (besides your fingers!) to properly tighten and use. These fittings often come in a variety of polymers, including PEEK, PTFE, Tefzel, Delrin, PPS, polypropylene, and others, for maximum cost and solvent resistance flexibility.
In order to properly use stainless steel fittings, the ferrule portion of the fitting must be swaged — or permanently attached — to the tubing it is connecting. To appropriately swage the fitting to the tubing, we recommend the following procedure:
Because the ferrule is permanently attached to the tubing, and because of standard machining tolerances, we highly recommend that any pre-swaged stainless steel fitting only be used in the mating port into which it was initially swaged. Failure to do this may result in dead volume or solvent leakage.
We have an excellent resource on making connections properly. Our Fittings 101 Guide includes descriptions of all the different liquid connection types that you are likely to encounter to enhance your fluidic system design.