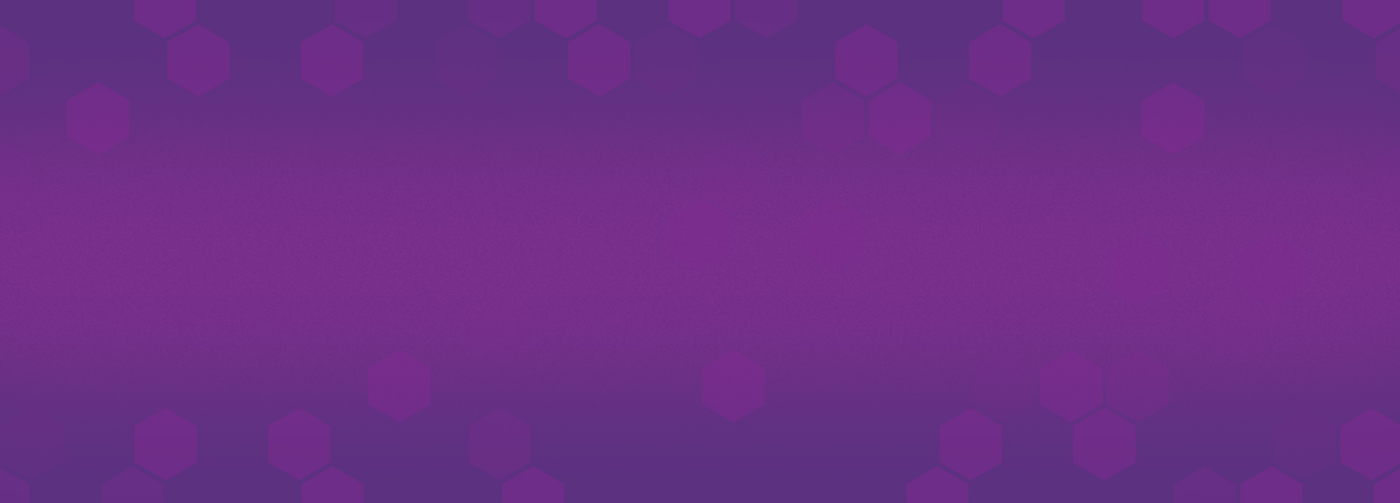
*Pictured left to right in the feature photo— Rylan Hodgson, Andrew Korts, and Corey Phung
IDEX’s collegiate opportunities and internships are designed to provide opportunities for exposure to a variety of real-world experiences. The goal is to enable insights that allow you to round out your areas of expertise and position you for expedited career growth.
Over the course of the summer, interns complete an important project for their assigned business unit. At the end of the summer, interns participate in professional development and present their ideas and results to leadership. This summer our Life Science Optics business line hired three interns for our Coating and Metrology teams. Here is what Rylan, Andrew, and Corey said about their experience with IDEX Health & Science.
“I spent the first few weeks of the summer in the Metrology cell measuring finished filters using spectrophotometry and interferometry. I learned a lot about optical testing instruments, and even more about the manufacturing process in general. One of my favorite larger projects from this summer was reviewing product data and automating data analysis using Excel’s Visual Basic coding language. I learned about features and uses for Excel that I didn’t know were possible thanks to my amazing colleagues. I then had the chance to work with application designs while redesigning a software application used in the Metrology cell. The best part about this summer was being able to work with and learn from coworkers with decades of experience in the field,” said Rylan Hodgson, Manufacturing Intern
“This summer I worked in the Metrology Department. I mainly employed various spectrophotometers and interferometers for analyzing optical filters to ensure that they were up to specification. Being an Optical Engineering Major, it was fun to work alongside machines whose principles I learn about every day in school. This summer has been a great chance to solidify what I know and figure out what I still need to learn. I also had the opportunity to shadow and work with some of the engineers. From them, I got a more holistic view of what it was like to be an engineer— responsibilities on the factory floor, engineering constraints, the lifetime of a product within the facility, and a few very interesting projects that some of them are working on. Lastly, I am grateful that I was able to strengthen my interpersonal communications skills within a manufacturing environment, learn how to ask the right questions, and expand my resource network,” said Andrew Korts, Coating Associate Intern
“Something I really enjoyed this summer was getting to learn how manufacturing processes are created and how each process is unique to each product. I learned that very small changes in a process can be a very big situation in the eyes of a manufacturing process. Each change must benefit the process as a whole and improve the efficiency on the operating floor. In addition, I learned how to analyze a process and confirm which parts positively affect the product yield and which parts of the process are negatively affected by the process yield. My internship consisted of 3 projects: a part marking project, a bevel chuck inventory project, and a label project. In the part marking project, I was tasked with creating fixtures for parts that needed to be caret marked on the side. By completion, we saw dramatic improvement in labor efficiency for this process. The bevel chuck inventory project consisted of creating a website that keeps the inventory of all bevel chucks on the floor, and their status. For the bevel chuck inventory, I worked closely with a software engineer and created a website that keeps the inventory of the bevel chucks. This project helped improve engineering efficiency, saving engineering time on each new product introduction. Also, this helped improve product yield on each work order by making sure the operator doesn’t use a defective bevel chuck on accident. Lastly, the label project had me work closely with a software engineer to create templates for a customer. This template allowed us to print labels on demand versus pre-printing labels. Printing labels on demand saves money and space. I am very thankful for my time here at IDEX Health & Science for the people that I met. There are lessons and techniques that I learned here that I know I will never forget,” said Sam O’Connor, Coating Engineer Intern
“I worked on a few things, including building optical metrology equipment, data mining production data, and various improvement projects. I also really enjoyed my hands-on experiences with production hardware. Overall, I dipped into a bunch of different small projects and I learned a ton,” said Corey Phung, Manufacturing Engineer Intern
Learn more about a career with IDEX Health & Science